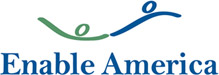
Job Information
Integra LifeSciences Sr. Quality Engineer in Anasco, Puerto Rico
Changing lives. Building Careers.
Joining us is a chance for you to do important work that creates change and shapes the future of healthcare. Thinking differently is what we do best. To us, change equals opportunity. Every day, more than 4,000 of us are challenging what’s possible and making headway to help improve outcomes.
ESSENTIAL DUTIES AND RESPONSIBILITIES
Develop and leads multiple activities and large complex projects (e.g. Validation Master Plan, CAPA Projects), as required.
Development of Quality project management of Six Sigma projects and quality improvement plans. Identify and implement opportunities for continuous improvement.
Prepare information for Quality Management Reviews and Operational Reviews such as: trend charts, Pareto Analysis, etc., as required. Perform and complete assigned complaints investigations, including but not limited to Product Failure Analysis and complaint documentation review (DHR, complaints history, products instructions, risk management, etc.) and prepare investigation reports.
Complete assigned Non-Conformance and CAPA investigations and prepare investigation reports.
Quality Problem Resolution by means of Root Cause/Problem Solving Analysis. Implementation of corrective and preventive actions for process related concerns.
Conduct assigned Supplier Audits and prepares reports and required documentation.
Development of risk management documentation (i.e. Medical Device Hazard Analysis, Process Failure Modes and Effects Analysis) for products manufactured, as required.
Participates in FDA inspections, ISO Certification and surveillance audits and customer audits as required.
Support to Calibration Area by reviewing/approving records and closing work orders in Maximo.
Develop statistically based sampling plans for in-process and final testing and inspections, and validations.
Development of process controls for new and existing equipment and/or processes.
Work on project teams with other internal departments, external vendors, and customers. Interact and coordinate activities, as required.
Interface with Engineering and Operations to ensure transfer to Production of new products are in accordance with approved data.
Review and approve validations and completion reports for new and existing products, processes and equipment. Provide statistical analysis of the data to support the reports.
Responsible for total Project Management in the generation and execution of validation protocols, Standard Operating Procedures, risk analysis, and validation project plans and quality plans for large and/or complex projects being headed by Quality Department. Oversee validation contractor resources, as required.
Prepare validation protocols (FAT/SAT/IQ/OQ/PQ/PV/CSV’s), execute validations and create completion reports. Provide statistical analysis of the data to support the reports.
Ensure that all projects, including appropriate documentation such as: protocols, technical reports, validation/quality plans, standard operating procedures, risk analysis, design control documents, drawings and specifications are generated in compliance with Integra's procedures, cGMP requirements and statutory requirements (US FDA, ISO, MDD and CMDR).
Recommend process/quality improvements as part of validation runs.
Generation of manufacturing/quality documents (i.e. Shop Orders, Specifications, Drawings, Inspection Criteria, etc.) necessary for the manufacturing and testing of validation products.
Develop and utilize a tracking system to facilitate prompt approvals of documents.
Develop and implement SPC control system with Manufacturing and Quality Control.
Work with project teams to develop Design of Experiments (DOE’s) and statistically sound tests for appropriate support of results. Ensure that all projects are in compliance with QSR (including Design Controls), ISO or other applicable requirements.
Support corporate or division Regulatory Affairs by providing information for submissions and Annual Reports.
Maintain fiscal responsibility and budget compliance.
Perform other related duties as required.
MINIMUM QUALIFICATIONS – Education and Experience
The requirements listed below are representative of the knowledge, skill, and/or ability required for this position.
BS in Chemical, Biomedical, Mechanical, or Industrial Engineering
5 to 7 years minimum experience in an FDA regulated environment.
ASQ Certified Quality Engineer (CQE) and/or Quality Auditor (CQA) preferred.
Experience with Quality System Regulation (QSR), ISO, Design Control and Process Validation guidelines.
Able to develop technical documentation such as: Validation Protocols, Technical / investigation reports, SOP, Validation Plans, Change Controls, and others.
Will have a fundamental understanding of a quality system and its development, documentation and implementation to domestic and international standards or requirements.
Will have a basic understanding of the audit process including types of audits, planning, preparation, execution, reporting results and follow-up.
Will be able to develop and implement quality programs, including tracking, analyzing, reporting and problem solving.
Will be able to plan, control and assure product and process quality in accordance with quality principles, which include planning processes, material control, acceptance sampling and measurement systems.
Will have basic knowledge of reliability, maintainability, and risk management, including key terms and definitions, assessment tools and reporting.
Will have a thorough understanding of problem-solving and quality improvement tools and techniques. This includes knowledge of management and planning tools, quality tools, preventive and corrective actions, and how to overcome barriers to quality improvements.
Will be able to acquire and analyze data using appropriate standard quantitative methods across a spectrum of business environments to facilitate process analysis and improvements.
Problem solving and analytical thinking skills
Strong Project Management skills
Strong skills in technical writing
Knowledge in Lean and Six Sigma concepts
Knowledge of statistical techniques: SPC, DOE, Process Capability and Gage R & R, etc.
Use of statistical process Minitab tools is preferred.
Working knowledge of computers and business software (MS Office, MS Project, VISIO) required.
Experience in biomaterials preferred.
Experience in cGMP, cleaning methods and validations preferred.
Ability to interact cross-functionally required.
Strong interpersonal skills
Teamwork oriented and self-starter
Fully bilingual (English/Spanish)
Integra LifeSciences is an equal opportunity employer, and is committed to providing equal employment opportunities to all qualified applicants and employees regardless of race, marital status, color, religion, sex, age, national origin, sexual orientation, physical or mental disability, or protected veteran status.
This site is governed solely by applicable U.S. laws and governmental regulations. If you'd like more information on your rights under the law, please see the following notices:
EEO Is the Law (https://www.eeoc.gov/laws/index.cfm) | EOE including Disability/Protected Veterans (https://www.eeoc.gov/eeoc/publications/ada_veterans_employers.cfm)
Integra LifeSciences is committed to provide qualified applicants and employees who are disabled veterans or individuals with disabilities with needed reasonable accommodations in accordance with the ADA (https://www.eeoc.gov/eeoc/publications/fs-ada.cfm) . If you have difficulty using our online system due to a disability and need an accommodation, please email us at careers@integralife.com or call us at 855-936-2666.
Integra - Employer Branding from Integra LifeSciences on Vimeo (https://player.vimeo.com/video/265760526)
Integra LifeSciences
-
- Integra LifeSciences Jobs