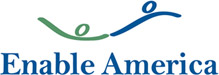
Job Information
Pilgrim's MAINTENANCE MANAGER - Protein Conversion in Broadway, Virginia
Maintenance Manager – Protein Conversion
At Pilgrim’s, Safety Is A Condition , which means the safety of our team members comes first - always.
JOB PURPOSE
Directs and manages a team of maintenance personnel in a protein conversion facility to include maintenance supervisor, parts room attendant, and wastewater supervisor as well as mechanics , rendering and steam generation operation . Leads and supervises capital expenditures, projects and facility expansions while maintaining production efficiencies within budgetary parameters. Drives continuous improvement within the maintenance organization.
Responsibilities
Successfully executes all site projects using expertise to manage projects and/or programs within desired budget, timelines, and quality parameters.
Communicates and promotes the business strategy and clarifies the actions needed to implement it within the area of responsibility; motivates and ensures the team’s commitment to achieving the organization's business goals.
Understands and is knowledgeable of all local, state, and federal laws and regulations, including Occupational Health and Safety Administration (OSHA), Food Safety and Inspection Service (FSIS), and Environmental Protection Agency to ensure environmental, health, and safety processes are executed and in compliance.
Acts as the business unit expert to analyze data trends to help guide decision-making at a senior level.
Estimates the labor required to perform maintenance tasks, define problems, collect data, establish facts, and draw valid conclusions.
Acts as the business unit’s expert to interpret an extensive variety of technical instructions in mathematical, diagram, written and/or verbal form and work with several abstract and concrete variables.
Collaborates with senior management, contractors, vendors, and suppliers to support maintenance and engineering projects
Propose, design and introduce new equipment needed to automate processes within the facility to maximize production and labor efficiencies while improving product quality.
CRITICAL COMPETENCIES
Plans and aligns
Plans and prioritizes work to meet commitments aligned with organizational and production goals.
Optimizes work processes
Knows the most effective and efficient processes to get things done, with a focus on continuous improvement for the operation.
Strategic mindset
Sees ahead to future possibilities and translates them into breakthrough strategies.
Financial acumen
Interprets and applies key financial indicators to make better business decisions.
Manages complexity
Makes sense of complex, high quantity, and sometimes contradictory information to effectively solve problems.
Education & Experience
To perform this job successfully, an individual must be able to perform each essential duty/function satisfactorily. The requirements listed below are representative of the environment, knowledge, skills, and/or ability required or preferred. Reasonable accommodations may be made to enable individuals with disabilities to perform the essential functions as listed below.
Bachelor's degree in mechanical or electrical engineering preferred or an equivalent combination of education and experience.
Minimum of 5 to 10 years of maintenance and engineering experience or similar position in a fresh protein harvest facility.
Wide and deep management experience providing expert competence over 5 years with demonstrated leadership and people development skills.
Experience interpreting strategy and policy in order to set and deliver objectives within medium to long timeframes.
Strong electrical background (PLC, instrumentation, industrial electrical experience) preferred
Demonstrated history of work primarily disciplined in the rendering and animal food sector.
EOE/Vets/Disabled