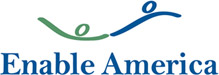
Job Information
AeroFarms Maintenance Team Leads in Danville, Virginia
Maintenance Technical Team Lead is responsible to direct and oversee the maintenance shift team through effective leadership in all aspects of the maintenance department. Team Lead will perform training for other members of the maintenance team, along with routine troubleshoot, dismantle, inspect, repair, modify, rebuild, service and adjust all types of plant equipment.
Hours of Work:
· 2nd Shift: Work hours are Monday thru Friday 2:00-10:30 pm. Weekend coverage will be necessary on 1 of 4 weekends.
· 3rd Shift: Work hours are Monday thru Friday 10:00-6:30 am. Weekend coverage will be necessary on 1 of 4 weekends.
Shift Team Lead Job Responsibilities:
· Directs, administers, and controls hourly operations and activities of the maintenance shift team to support the operations of all plant equipment and facility issues.
· Assign work orders and PM’s to team members and ensure team member has necessary instructions, parts and training to perform work. Team Lead will monitor deadlines to ensure work orders are completed on time.
· Responsible to update any parts issues or parts inventory use in Upkeep to ensure parts inventory is accurate.
· Address all equipment and reliability issues affecting operations in a timely manner to minimize downtime and ensure a safe working environment for all employees.
· Ensures compliance with established company operating procedures
· Participates in the implementation of company initiatives and strategies.
· Implements, disseminates, and administers operations strategies and objectives to ensure the achievement of the maintenance department goals and objectives.
· Formulates location-specific and area quality goals and action plans to achieve quality standards.
· Provides leadership, support, and guidance to team members, as well as informal feedback on an ongoing basis to identify and develop talent.
· Contributes to a strong and robust communications process between all managers and staff within the area and across the division as needed.
· Ensures all employees receive the appropriate training and education according to policies and procedures including ongoing compliance training
Other routine Maintenance Technician deliverables are:
· Print reading to include electrical and hydraulic prints and schematics.
· Experience with AC/DC motors and drives, 110-480Vac Circuits, thermocouples, single and three-phase circuits, HVAC, reversing starters, and personnel computers.
· Communication skills both verbally and written.
· Troubleshooting, conduit threading, bending installation, wiring installation, electronic repair skills.
· Work with Packaging Technician and Farm Equipment Operators on establishing equipment home-settings and maintaining baseline conditions.
· Operation of equipment including a forklift, man lift, aerial lift, overhead cranes, and mobile cranes.
· Use of Voltmeters, calibration of equipment, oscilloscope leaders, PLCs, PCs.
· Calibration of all types of electrical equipment and knowledge of HVAC systems.
· Must exercise good judgment at all times and can complete assigned tasks, as well as breakdown repairs without direct supervision.
· Ability to manage multiple tasks and prioritize to ensure minimum interruption to the process.
· Work in an environment with a temperature that varies from extreme good to moderate. Exposure to farm environment: 70-78F at 65% RH in grow rooms and cold rooms at 33-36F, some areas are wet, dirty, and have some chemical exposure which is protected by PPE. Building maintenance with outside weather conditions up to (110 degrees), and as low as (10 degrees cold).
· A high to a very high degree of concentration is required.
· Strenuous physical activities including a lot of walking, climbing ladders and stairs, entering restricted areas, heavy lifting (50 lbs. or more), and working in high areas.
· Responsible for the maintaining and sanitation of all work tools.
· Able to work safely and follow all safety requirements to ensure safety to self and co-workers
Qualifications:
· Two year associate degree in a technical discipline or higher level of prior relevant experience performing industrial maintenance and training.
· Minimum of 3 years as Team Lead of other technical staff is highly desirable. Bachelors or Associate degree in Business Management a plus.
· Minimum of 3 years industrial maintenance, electrical, and/or plumbing within an automated manufacturing facility is required.
· Successful completion of an approved Heavy Industry Apprentice Program helpful
· Knowledge of and ability to troubleshoot, program, and repair PLC controlled manufacturing processes highly desirable.
· Complete training and or studies to learn how to read and troubleshoot PLC programs
· Knowledge of and prior experience with industrial robotic automation
· Print reading including electrical and hydraulic prints and schematics.
Skills:
· A high to a very high degree of concentration is required.
· Ability to manage multiple tasks and prioritize to ensure minimum interruption to the process.
· Communication skills both verbally and in writing.
Internal candidates seeking a promotion must have completed a minimum of six months in their current role before becoming eligible for consideration.
In accordance with organizational protocol, employees will at times be required to fill absences in the operation process that are equal to or lower than their positional hierarchy. Additionally, if an employee is absent, the role of the absent employee is to be completed by their immediate superior.
*Please note that AeroFarms does not work with any external staffing/recruitment vendors. Any unsolicited resumes shared with the AeroFarms team will be considered property of AeroFarms and no recruitment fees of any kind will be paid or owed unless an existing recruitment agreement exists alongside with specific engagement for the role in question.
Powered by JazzHR