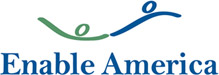
Job Information
In-Situ Inc. Production Supervisor-2nd Shift in Fort Collins, Colorado
Production Supervisor - 2nd Shift
Position: Production Supervisor - 2nd Shift (3pm-11:30pm) Reports To: Director of Operations Department: Operations Location: Fort Collins, Colorado
GENERAL PURPOSE: The Production Supervisor-2nd shift is responsible to lead In-Situ's Production team to meet the needs of both internal and external customers and to drive continuous improvements as it relates to Safety, Quality, Delivery, and Productivity. The Production Supervisor is also responsible to develop both talent and processes to attain In-Situ's growth goals through the utilization of lean manufacturing tools and principles.
ESSENTIAL DUTIES/RESPONSIBILITIES: Drive a culture of winning and continuous improvement through establishing and managing clear expectations from everyone on the team utilizing Toyota Production System/Lean Manufacturing Principles Ensures all associates are knowledgeable of, and comply with, all work policies. Holding the team accountable to safety and standard work expectations Works with Planner to create plan and set clear expectations for operators around daily output to maintain on time delivery goals to customers and protect productivity. Works with Planner and Materials Manager to evaluate customer orders to ensure that labor and materials are available to meet the delivery expectations. Responsible to understand the Takt time and Cycle time of each product line so that resources can be scaled to meet on time delivery goals. Protects and improves the team's productivity through continuous improvement and lean tools. Responsible for driving data-driven action plans to improve standard Work & SQDC performance Leads cell board meetings and daily stand-up meetings when Director is unavailable. Works closely with Materials Manager to ensure that material is presented and transacted according to In-Situ's materials policies and best practices. Responsible for the cross-training operators so that production resources can be dynamic. Owns the cross-training plan, setting expectations with operators on training. Enlists all associates in the commitment to excellence, leading by example. Subject matter expert for Production process flows. Develops future state vision for the Production process flow and works with cross functional teams on the development of tools and processes. Responsible for OOB failures relating to Production. Solves problems in areas of responsibility using data-driven process and implements corrective action that eliminates the problems. Works with Process Engineers and Operators to drive process and margin improvement activities Evaluate associate performance and conduct reviews. Coach, train, and counsel associates to improve performance. Responsible to support In-Situ's cycle count program including the completion of counts and count accuracy. When counts are inaccurate, to drive to root cause and implement corrective actions. Other duties as assigned
MEASURES OF PERFORMANCE Safety - #1 priority. Directly responsible for ensuring a safe production environment. Quality - #2 priority. Ensure standard work processes are being followed and quality objectives are being met. Delivery - #3 priority. Directly responsible for achieving on-time delivery goals against customer request dates. Minimize past due backlog while delivering in competitive lead-times. Cost - #4 priority. Improve direct labor productivity and help drive down manufacturing overhead.
OTHER DUTIES/RESPONSIBILITIES: Maintain close working relationships with internal departments. Drive continuous improvement to the processes that support the business. Support material handling functions in the event of absences. Participate in internal and external training and workshops. Actively pursue on-going personal development of relevant knowledge and skills. Other needs as directed.
SUPERVISORY DUTIES:
Non-exempt full-time employees and temporary staff a necessary.
JOB QUALIFICATIONS: Leader of people Lean Manufacturing skills Excellent communication skills Demonstrated change agent Data and Fact-Based problem-solving skills Scheduling and planning skills Time management skills Computer office skills 5 years manufacturing experience with 1 year in a leadership position Applicants must be eligible to work in the United States of America
Personal Attributes Sense of urgency Excellent written and verbal communications skills Ability to inspire excellence among team members Process oriented Ability to lead and embrace change Leader skills that develop team accountability, fair treatment of employees, recognition and open communication.