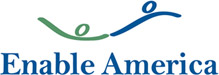
Job Information
Krupp Bilstein of america, Inc Operational Excellence (OPX) Engineer in Hamilton, Ohio
Company thyssenkrupp Bilstein of America, Inc. is a world class manufacturer of suspension solutions headquartered in Hamilton, Ohio USA. thyssenkrupp Bilstein of America supplies products to a wide range of Original Equipment Automotive Manufacturers as well as Aftermarket and Motorsports customers. Our Aftermarket operations are based out of Poway, CA and our Motorsports operations are based out of Mooresville, NC. For decades, the name BILSTEIN has been synonymous with high tech in suspension design, driving comfort, and safety. In order to expand this position BILSTEIN became a division of thyssenkrupp Technologies AG in 1988, and a wholly owned subsidiary in 2005. This partnership has enabled us to continue the BILSTEIN tradition of excellence. Your responsibilities Summary: The Operational Excellence (OPX) Engineer identifies and implements activities that improve the organizations performance; including, safety, sustainability, quality, delivery, and cost. Facilitates continuous improvement by personally leading, challenging, teaching and supporting the organization's goals. Evaluates and improves manufacturing and office operations to drive cost savings and productivity. Essential Duties and Responsibilities: Maintains a safe working environment by complying with all safety and environmental policies in the workplace. Advocates for and promotes a safe work environment by reporting Near Misses and/or other safety and environmental hazards, wearing all required PPE and encouraging others to do the same. Implements solutions related to the organizations strategic goals, drives completion of action plans, executes projects and shares best practices with the extended organization. Keeps aware of manufacturing operations including analyzing short and long term process trends, production output, labor efficiency and drives improvements from the data. Develops and manages operational breakthroughs in performance by leveraging industry best practices, key innovations, and other methods in order to accelerate current performance. Supports and applies lean manufacturing principles to improve the organizations productivity. Justifies investment for improvements using validated data for cost savings. Applies statistics and analysis for data driven decision making. Facilitates monthly cross-functional workshops on continuous improvement analysis. Conducts audits of 5S, Idea generation, and other lean activities to ensure programs are understood and being followed to add value. Measures and analyzes resource productivity using time and motion studies and makes recommended changes to flow that will ultimately improve KPI performance Addresses stakeholder needs proactively to improve our position. Facilitates workshops for the designs and layout of equipment, materials, and workspace to illustrate maximum efficiency. Finds and initiates valuable projects based on stakeholder input and data Ensures compliance and safety of all activities within the organization standards and policies. Performs all other duties and responsibilities as assigned. Your profile Qualifications & Experience: Experience with Six Sigma and Lean Manufacturing. Six Sigma certification preferred. Exceptional communication and presentation skills to all audience levels. Experience leading teams through improvement projects, problem solving, brainstorming Strong skills in data analysis, statistics, and manufacturing systems Experience driving improvements in a high volume manufacturing environment. Ability to balance multiple projects and shift priorities to meet business needs. Can quickly build strong relationships and trust to affect difficult change. Successful track record of leveraging operational excellence tools to drive improvements. Solid project management experience and ability to work with all levels within an organization from