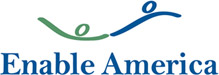
Job Information
GE Appliances, a Haier company Senior Advanced Manufacturing Engineer in Louisville, Kentucky
Job Location
USA, Louisville, KY
Job Posting Title
Senior Advanced Manufacturing Engineer
The Challenge
The Advanced Manufacturing Engineer (AME) is a member of a product line AME team responsible for providing manufacturing support New Product Introduction (NPI), Cost-Out and Plant Productivity projects. The AME shall develop, manage and execute capital equipment and high volume manufacturing process projects to meet required budget and launch schedules. The AME is a key liaison between NPI programs and the factory operations teams; ensuring plant priorities and objectives are clearly understood and considered. This includes providing input for design for manufacturability, applying lean principles to process designs and transferring process knowledge to the applicable factory personnel.
What you will Do
Technical Responsibilities:
· Coordinate and manage capital equipment procurement projects:
Including specification development utilizing GEA & industry standards,
supplier selection, early supplier engagement, technical reviews, factory
layout development, installation and qualification of equipment. Ensure
all tooling and equipment is reliable and robust and designed to
maximize Overall Equipment Effectiveness (OEE).
· Own the program metrics as applicable to your assigned projects: capital
equipment & tooling budgets, program schedule, reliability, quality and
labor targets. Work with the program team to perform trade-off analysis on competing metrics if necessary and drive decisions based on overall business impact. · Facilitate/lead the use of the Production Preparation Process (3P) and Lean manufacturing principles while developing manufacturing equipment and processes. Utilize cross-functional participation to ensure that the equipment and processes are compatible with the entire value stream. Efforts should include: right-sized equipment, workstation design, material presentation, standard work and single piece flow.
Standards and Compliance:
· Ensure all equipment executed in GEA factories comply with Industry
and Governmental Environmental Health & Safety (EHS) standards.
· Utilize Human Organizational Performance (HOP) principles to ensure
that all equipment / tooling / processes are implemented with the health
and safety of the operators in mind.
· Work with functional leaders to ensure equipment & processes support
business initiatives of Bill of Process (BoP), Lean Manufacturing,
Ergonomic Design and Total Productive Maintenance (TPM)
Cross-functional Work and Leadership:
· Work with factory operations and Lean teams to understand the Value
Stream and how your projects impact this. Ensure material flow,
workstation set up, model mix, etc. are considered when workstations /
equipment are designed.
· Utilize the 9-Step Process for tooling and equipment design; consult
Critical Process leaders as applicable to ensure development of robust
processes for part / product generation. Work with cross-functional team
to develop Manufacturing Control Plans (MCP) and Manufacturing
Control Instructions (MCI).
· Work with design team to ensure Design for Manufacturing & Assembly
(DFMA) is considered on part design.
· As a senior professional, participate in growing the AME organization’s
capability. This includes mentoring, guiding and helping more junior
team members as well as adding to the body of knowledge of the
department (training, developing new manufacturing processes,
supporting Hoshin objectives, etc.)
What you need to Succeed
Preferred Qualifications:
· BS degree in Mechanical, Industrial or Manufacturing Engineering
· Experience with assembly line design, automation and customized fabrication equipment and manufacturing processes
· Experience with implementing Lean process improvement in a manufacturing operation
· Prior NPI program experience
· Six Sigma Certification
· Proficient in MS Office, MS Scheduler (or equivalent) and AutoCAD
Minimum Qualifications:
· Bachelor of Science Degree in Engineering or related discipline OR equivalent hands on experience in technical/manufacturing disciplines
· 7+ years of experience with procurement, testing, installation of manufacturing equipment and process improvement
Position Requirement
· Experience managing capital equipment procurement projects: Including specification development, supplier selection, technical reviews, installation and qualification of equipment
· Prior experience in a large scale manufacturing environment
· Experience with Lean manufacturing principles
· Ability to work in large cross-functional teams and at multiple levels in the organization (both salaried and shop floor operators / skilled trades team members)
· Ability to communicate effectively and be an agent for change.
· Good organizational, project management and presentation skills to interact with all levels within the organization and with suppliers and vendors
· Demonstrated ability to take ownership of cross-functional program deliverables and ability to drive decisions based on the overall benefit to the company
· Ability to mentor, grow more junior members of the team and add to the body of AME knowledge for the business
Working Conditions:
· Working conditions are normal for a high volume manufacturing environment.
· Work may involve lifting of materials and product up to 30 pounds and working in and around heavy equipment.
· Working in this environment requires the use of safety equipment to include but not limited to; eye safety glasses, hearing protectors, work boots, and hardhats.
· These roles will require frequent walking in a manufacturing plant environment.
· 20-30% travel may be for domestic and/or international travel to supplier sites/ plants, etc.
· Hours & Weekends: Working off-shift and weekends will be required.
GE Appliances is an Equal Opportunity Employer. Employment decisions are made without regard to race, color, religion, national or ethnic origin, sex, sexual orientation, gender identity or expression, age, disability, protected veteran status or other characteristics protected by law.
GE Appliances, a Haier company
-
- GE Appliances, a Haier company Jobs